- Water Well Pump System Design
- 2.5 Pump Design Water Supply System
- Water Pumping System Design
- Water Pump Design Pdf
Introduction to general design of domestic service water supply systems - with pressurized or gravity tanks
2.1 water demand 8 2.2 water distribution systems 10 2.3 water distribution modeling 11 2.4 pumps 13 2.5 valves 17 2.6 tanks and reservoirs 18 2.7 controls devices 19 2.8 epa 20 3.0 laying out a project 21. United Water New York Conceptual Design Report Haverstraw Water Supply Project Black & Veatch Project No. 146323 Page. 1 Section 3. Raw Water Supply and Storage 3.1 Plant Capacity and Flow The water treatment plant will be constructed in three (3) phases with an initial production capacity of 2.5.
Acknowledgments This is the fourth edition of the Water System Design Manual.Many Department of Health (DOH) employees provided valuable insights and suggestions to this publication. Pressure booster systems for drinking water, fundamentals 4 2. Calculation example: Drinking water supply system for a residential building 8 2.1 Calculating the flow rate of a pressure booster system 9.
The purpose with a domestic service water supply system is to provide consumers with enough hot and cold water.
In old buildings it is common with gravity storage tanks on the top floor of the building. More commonly used in new systems are pressurized tanks and supply pumps.
Domestic Water Supply with Gravity Tank
Domestic water supply system with gravity tank:
For proper operation of the system the gravity tank is located at least 30 ft or 10 m above the highest outlet or consumer. In taller buildings pressure reducing valves are required in the lowest floors before the fittings.
The volume of a gravity tank must be designed to compensate for limited capacity of a supply line. The tank fills up when the consumption of hot and cold water is lower than the capacity of the supply line - and the tank is emptied when the consumption is higher than the capacity of the supply line.
A drawback with the open gravity tank on the top floor is the potential danger of freezing during winter conditions. Huge tanks will also influence on the construction of the building.
Domestic Water Supply with a Pressurized Tank
Domestic water supply system with pressurized tank:
The pressurized tank is partly filled with air (or gas) behind a membrane. The air compensates for pressure variations during consumption and when supply pump starts and stops.
A pressurized tank has a limited compensating capacity for the shortage in a main supply line.
Estimating Required Buffer Tank Capacity
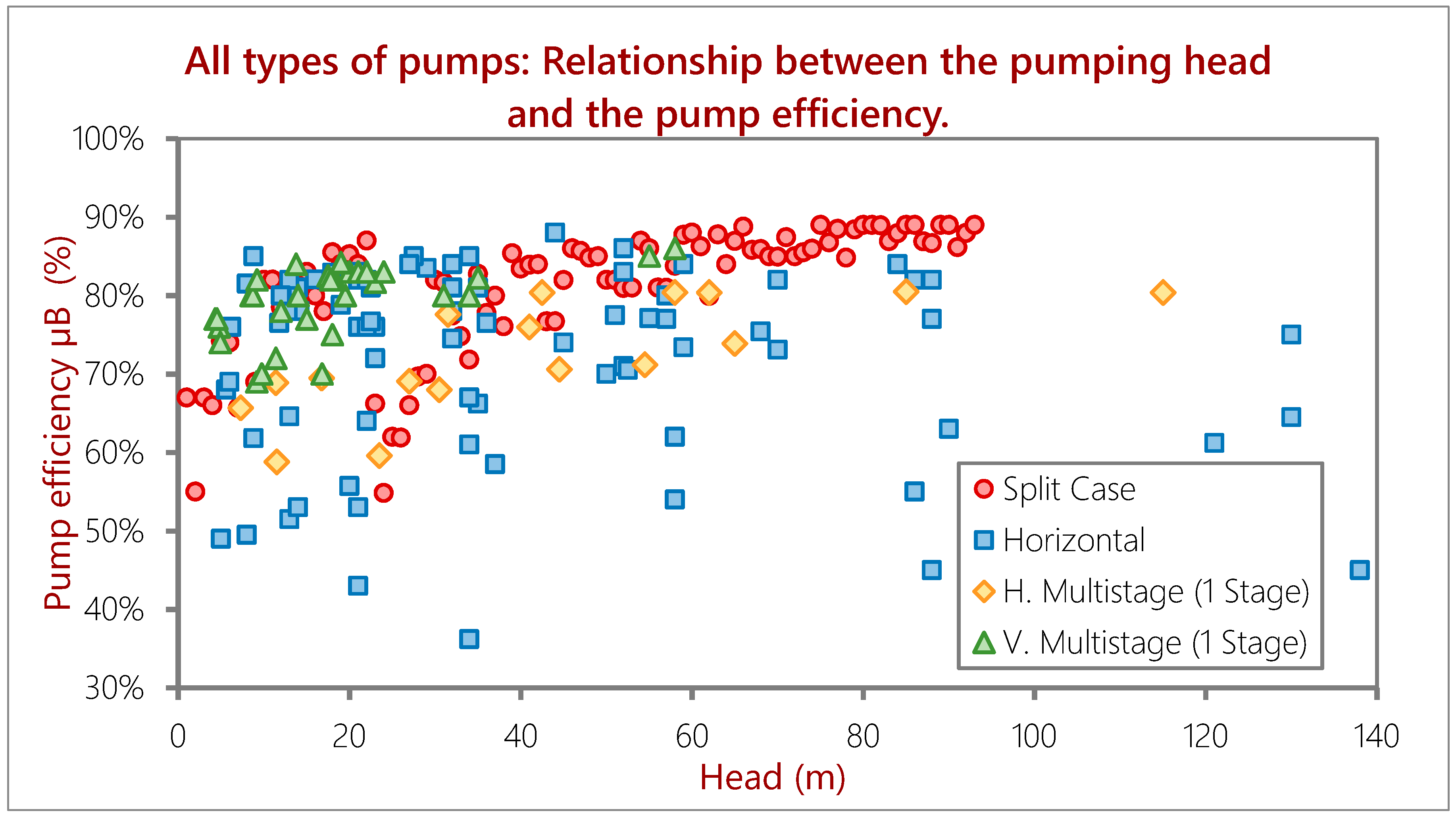
You are free to use the template bellow as a tool to estimate required buffer capacity in a water supply system. Log in to your Google Account to make your own copy to modify of the template. Alternatively - you can also save the Google Spreadsheet to your computer as a xls file.
Related Topics
- Water Systems - Hot and cold water service systems - design properties, capacities, sizing and more
Related Documents
- Cold Water Storage Capacity - Required cold water storage capacity - commonly used fixtures and types of buildings
- Cold Water Storage per Occupant - Cold water storage for occupants in common types of buildings as factories, hospitals, houses and more
- Cross-Contamination Control - It is fundamental to keep the potable water in the water supply systems uncontaminated
- Domestic Hot Water Service Systems - Design Procedure - Design procedure for domestic hot water service systems
- Domestic Water Supply - Lime Deposits - Lime deposited vs. temperature and water consumption
- Hot and Cold Water Pipe Sizing - Recommended dimensions of hot and cold water pipes
- Hot Water Circulation Return Pipe - Hot water can be circulated through a return pipe if it's instantly required at the fixtures
- Hot Water Supply - Fixture Consumption - Design hot water consumption of fixtures - basins, showers, sinks and baths
- Legionella - Legionella pneumophila - bacterium that thrives in water supply systems and air conditioning systems - causing the Legionnairs disease
- Online Design of Water Supply Systems - Online design tool for a water supply system
- PE Water Supply Pipes - Properties - Nominal pipe size, outside diameter, wall thickness, weight and working pressure
- Sizing Domestic Hot Water Heaters - Domestic Hot-Water sizing equations - heating capacity, recovery rate and power supply
- Water - Human Activity and Consumption - Activity and average water consumption
- Water Distribution Pipes - Materials used in water distribution pipes
- Water Service Pipe Lines - Water service pipe lines extends from the potable water source to the interior of buildings
- Water Supply Pipe Lines - Sizing - Sizing of water supply pipe lines
- Water Supply to Public Buildings - Required water supply to public buildings
- Yard Fixtures - Water Consumption - Water consumption in garden fixtures
Tag Search
- en: service water supply domestic gravity pressure tank
Part 14(c)—Submersible Pump Design, Part 3
By Ed Butts, PE, CPI
In these final two installments of this series on designing a submersible pump system we will conclude with a discussion on the design and sizing of the submersible motor and drop cable for our example, along with a complete review of the techniques used for designing submersible pump systems.
Electrical Acronyms and Definitions
We will reference several standards used for electrical design in the next two columns. The first and most common is the National Electrical Code (NEC) issued by the National Fire Protection Association as NFPA Standard 70. The NEC is regarded as the governing electrical code for use in the United States, but many states or localities also add revisions and amendments to the code applicable to their area only. The NEC is updated every three years, with the most recent edition issued in 2017.
The second acronym we will commonly use is NEMA standards. NEMA represents the largest electrical trade association in the United States and is short for the National Electrical Manufacturers Association. NEMA standards are available and recognized for numerous components and classes of electrical equipment including motors, enclosures, controls, generation, transmission, and distribution equipment.
In addition to NEMA, many electrical standards are now parallel to another group called the International Electrotechnical Commission (IEC). The use of either NEMA or IEC standards are generally recognized by most governing and inspection authorities in the United States.
Although the standards for most electrical equipment are established by NEMA and IEC, most electrical equipment must undergo a rigorous testing and certification procedure to ensure the equipment is rated for the intended application and will not represent a fire danger when used in approved environments. Most research, testing, and product certification in the United States is conducted by one or more of three agencies: Underwriters Laboratories (UL), Canadian Standards Association (CSA), or the Electrical Testing Laboratories (ETL).
Typically, if the electrical device or component complies with the applicable specifications and passes the testing procedures, the device is either listed or recognized for use. Although most states and localities recognize testing and approval from any of the three laboratories, there is no specific guarantee of this uniformity for any individual state or locality. Therefore, the reader is cautioned to fully investigate and verify whether any electrical component or system is approved for the intended use and application in their region before applying or installing.
Before we start a design process, let’s review the exact electrical characteristics from our original design example (Figure 1).
Step 1: Determine voltage and phase (1a) and/or system load (1b)
This first step may seem confusing to many, but which of the two steps, 1a or 1b, is the actual first procedure depends on several factors. Chief among these is whether the installation is a retrofit or replacement installation with the same or more horsepower on an existing power supply, or a new installation involving a new electrical service.
When applying a replacement or new submersible motor on an existing service, then step 1a is the most logical first step. If a new electrical service or generator operation is required, then step 1b is generally the first step to allow sizing of a new service by the utility or a generator, if used.
Step 1a: Voltage and phase
Since our example situation already details the system voltage, phase, and available current, much of the work needed for a new installation is complete. The information above on the electrical power supply is critical for the proper design and application of the various electrical components, particularly the submersible motor, drop cable, and controls used in the system.
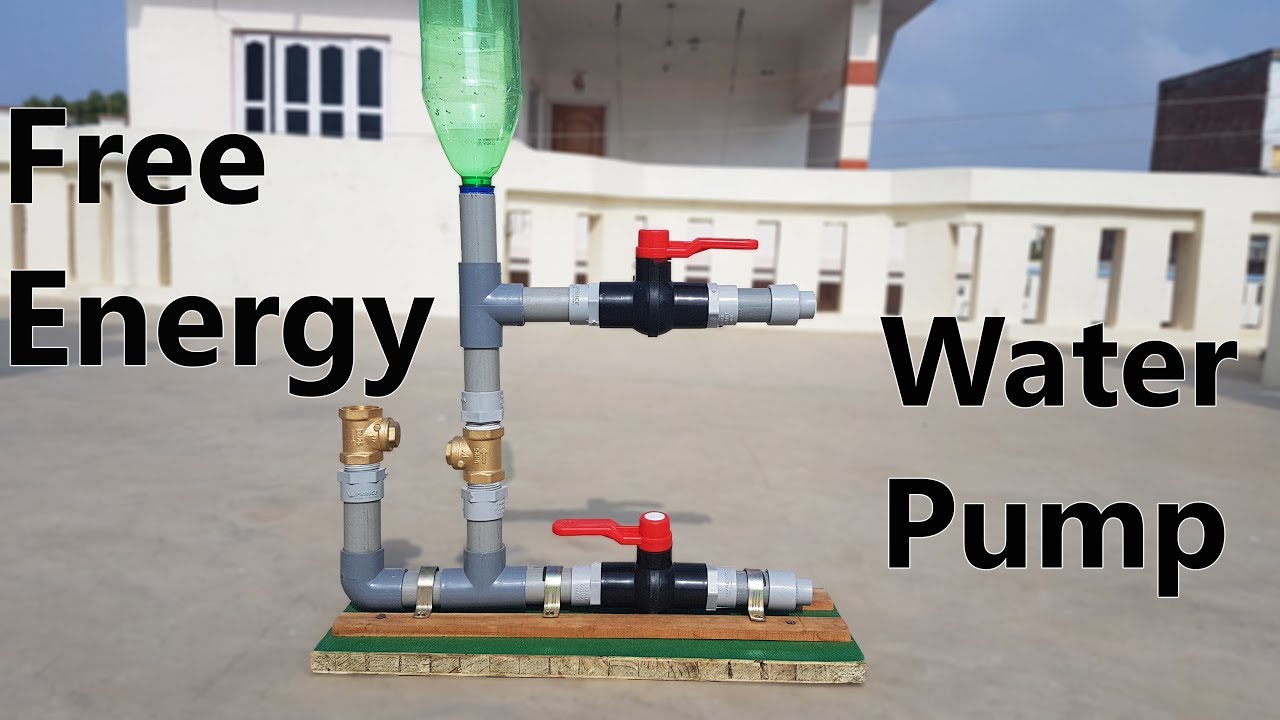
Although having an advance notice of the technical data regarding the electrical service and installation is important knowledge for all alternating current (AC) motors, there is probably no other type of motor where this is more important than with a submersible motor.
Since most submersible motors are designed for a single voltage and phase application, the most obvious initial design element to know is the available voltage and phase. For our design example, it can be seen the electrical service consists of a 200-amp, 480-volt, AC, 3-phase service with 160 amps of available full load current capacity.
In theory, this level of power is capable of operating up to a single 150 HP motor or a group of three 40 HP motors (156 amps). For an installation using a submersible motor, not much can proceed until the designer is satisfied he fully recognizes and understands the voltage and phase the serving utility or a generator will provide to the site.
Although it may seem contrary to logic for the voltage and phase to be the first criteria, in many parts of the country, particularly remote rural areas, the availability of higher voltages or polyphase power may be limited or not possible at all. Therefore, verifying these design factors with the utility or generator supplier is generally my first step. Table 1a displays the standard low voltage (<600 volts) supplies used in the United States.
Although U.S. power systems are designed for 60 hertz (frequency) operation, throughout the rest of the world there appears to be an endless array of possible voltage and frequency combinations. In 50 hertz regions, such as Canada and many international countries, virtually all power systems are of the 4-wire, grounded wye type, so a typical arrangement would be the use of a 220/380-volt AC power system.
In this case, as in the case of a typical 120/208-volt, wye, 60 hertz system in the U.S., the lower 220-volt source is only available for single phase and the 380-volt source is available as either single or three-phase power.
As a result of the voltage described as 220/380, specifications often require three-phase motors be wound for a dual voltage of either 220 or 380V. Although feasible to do this, it is usually unnecessary because the 50 Hz three-phase motors can only be operated on 380-volt, three-phase power. Since many submersible motors are designed to operate on either 50 or 60 hertz power, many motors are rated for 380- or 460-volt operation from either source.
Many submersible motor manufacturers also supply motors capable of operating on much higher voltages than the lower voltage systems below 600 volts. The application of these motors is their use with medium voltage sources between 1000 to 69,000 volts, with the most common voltage for three-phase motors either 2400 or 4160 volts. For those who occasionally deal with medium voltage applications, Table 1b details these two most common medium voltage systems used in the United States for larger motors.
For those charged with the responsibility of voltage selection or consulting, generally the best and most economical decision is to select a reasonable compromise between the system voltage, phase, and the current based on the connected load (horsepower) and total cost.
In other words, since current (amperage) often has the higher impact on component and system cost, selecting the higher voltage applicable with three-phase to lower the corresponding current is often the best overall choice. This must be tempered, however, with the knowledge a higher voltage or three-phase system may not be technically or economically available within a given region. This means you sometimes have no choice and just have to take what they will give you.
You may also have noticed the nominal voltage value for many three-phase systems is generally higher than the applicable operating (nameplate) voltage for a submersible motor, up to 5% for a 240- or 480-volt system operating a 230- or 460-volt motor, for example. Although certainly not universal, this discrepancy provides a built-in safety factor by providing a beginning voltage higher than what is required by the motor. I do not recommend, as a standard design course, to use these few percentage points of difference as anything but a compensatory “fudge factor” of voltage that will provide adequate starting and running voltage to the motor under all normal and abnormal conditions.
If the maximum 5% allowance for the drop cable loss is observed on a 480-volt system, then the remaining voltage at the motor terminals should equal around 456 volts, only 4 volts lower than the nameplate 460 voltage or 2 volts lower than a nameplate 230-volt value. This will help ensure the motor is operating within the allowable ranges and extend the life of the motor to the maximum possible.
Lastly, the type of power can also be critical to the performance and life of the motor and installation. The use of a 120/208- or 277/480-volt, 4-wire wye electrical service over a 240- or 480-volt “delta” or “open delta” power supply will almost always be preferred. If available, requesting a wye service, even if a higher cost, will pay long-term dividends to the customer and prevent a potential series of premature motor failures.
Even though this type of power is usually preferred, there are methods available to lessen a deleterious impact to a submersible motor from a delta power supply. We will discuss these methods in Part 4.
Step 1b: Determine the system load: motor horsepower and diameter
Once it has been determined the proper voltage and phase is available for the project, the next step is to move into the determination of the system load, specifically the motor’s required horsepower and diameter.
Obviously, since the wet end (pump) has already been selected, the motor must match the mounting and horsepower criteria required from the pump. In order to determine the motor’s required brake horsepower (BHP) first, we must repeat the step we previously used for the well pump:
Primary COS:
(1In this case, we have entered the exact efficiencies from our selected pump at both duty points.)
The calculated horsepower (41.5 BHP) at the primary condition of service (COS) could technically be provided from a 40 HP motor by using the 15% service factor (FLC × 1.15) available in most motors.
However, in order to extend the life of the motor to the maximum plus provide for any possible power or system anomalies, I recommend not using any of the allowable service factor for design of most municipal, commercial, or industrial applications. Therefore, for our example, a maximum input load of 41.5 BHP will require a 50 HP, 460 VAC motor.
Selecting the motor diameter is largely a choice between what is available for the horsepower and the size and mounting configuration of the pump. Referring to Table 2, a 50 HP submersible motor has four choices generally available: either a 6-inch or 8-inch-diameter motor for 3600 RPM (two-pole) applications, or an 8-inch or 10-inch-diameter motor for 1800 RPM (four-pole) applications.
Our selected pump is a 7-inch-diameter × 3600 RPM bowl assembly, and information from the manufacturer has informed us that either a 6-inch or 8-inch-diameter motor would be acceptable for this pump.
Although, once again often a personal preference, I would most likely opt to use a 6-inch-diameter motor for this application. Besides being a much cheaper motor and easier to get from most suppliers, I usually prefer not to use a motor larger than the pump I am connecting it to. The requirement for cooling at the VFD reduced flow of 156 GPM is met by either motor in the 12-inch well casing, so that factor is not a concern. Using the smaller motor will provide more annular space between the well casing and motor, plus prevent any implied momentum from misalignment or vibrational forces to the smaller pump due to the torque or possible misalignment between the larger motor and smaller pump.
In addition, it is also critical to verify any larger motor considered for attachment to a smaller submersible pump will not apply any excessive weight to either the mounting bracket or bowl assembly of the pump, and the shaft interconnection between the two components is the same.
It is important to note, however, my decision for our example is based on using a 6-inch-diameter motor with a single stator and rotor and not a tandem unit. If the needed 6-inch-diameter motor had to be constructed by using two 25 HP motors in series (a tandem unit), a common practice years ago, then I would have definitely opted for the 8-inch-diameter unit as I have personally observed many problems with tandem motors from electrical inconsistencies and imbalance between the two motors.
In summary, although the horsepower, and often the voltage and phase, is usually a requirement of the application, a choice can often be made in the pump and motor’s speed and diameter. This decision can only be made after evaluating all salient factors of the design including the installation parameters, annular well clearance, pump to motor mounting options (NEMA fit or not), motor starting and running characteristics, availability of new and replacement motors, and cost.
Step 2: Determine motor starting requirements
When considering operating an electric motor, it is not only important how well you can run a motor, but how easy it is to start one. Very often, the limiting factor with any single or polyphase electric motor is the ability to draw sufficient power from the line over the few seconds needed to generate the required torque and magnetizing current required to overcome the inertia of the pump and motor.
Water Well Pump System Design
With a submersible motor this is often an unforgiving element since the long lengths that often exist between the power supply and the motor can create enough of a voltage drop to prevent starting. In addition, the high current inrush, up to six to seven times the full load current, associated with the starting of any motor can also cause enough voltage drop to result in a local condition known as flicker.
Flicker is the momentary drop in voltage caused by a large inrush of current that can result in a brief loss of light intensity from fluorescent and incandescent fixtures. This condition is avoided by either providing adequate power to accommodate the high inrush current with a minimal voltage drop, or by lowering the starting current through a process called reduced voltage starting.
From our example, we know there is adequate power available to start up to a 50 HP motor without using reduced voltage starting. Therefore, we could have used a “direct on line (DOL)” also known as “full-voltage” or “across-the-line” starting method where the motor starts using full or 100% voltage under locked rotor amperage and accelerates up to full speed in a few seconds.
Full-voltage starting remains the most common method of motor starting and accounts for over 95% of the motor starting applications.
Although this would have been a feasible and lowest cost method of motor starting, in this case we designed for a primary and secondary design condition, which required using either a control valve or variable frequency drive (VFD) for flow and pressure control. Since a VFD was selected to provide variable speed operation, as a motor control this same unit also provides inherent reduced voltage starting and stopping, generally referred to as soft starting and overload protection.
Although the use of a VFD has become popular, there are still alternate ways to accommodate reduced voltage starting for submersible motors. Refer to Table 3 and Figure 2 for information and typical schematics on motor starting methods available for submersible motors.
Regardless of the method of motor starting selected, the proper knowledge of the motor’s locked rotor amperage is generally required for the utility to determine the allowable inrush current for the service. As an element of every motor’s nameplate and technical data, information regarding the motor’s “KVA Code” is available (Table 4). Code letters from A to R are shown with the accompanying KVA/HP range and the typical mid-range value.
To determine the approximate locked rotor current requires investigation or confirmation of the specific code letter. This value is usually available from either the motor nameplate or design data. As a shortcut, the following equations can be used to approximate the locked rotor amperage (LRA) for a three-phase motor:
200-volt LRA = Code letter value (use mid-range value) × Motor HP × 2.9
230-volt LRA = Code letter value (use mid-range value) × Motor HP × 2.5
460-volt LRA = Code letter value (use mid-range value) × Motor HP × 1.25
575/600-volt LRA = Code letter value (use mid-range value) × Motor HP × 1.00
For our design example with a 50 HP, 460-volt motor, the approximate 460 volt LRA is:
(from manufacturer data) Code Letter H. Use the mid-range value = 6.7 × 50 HP × 1.25 = 418.75 amps
Note that the above value is an approximation only and may vary ±2% from the actual value. Where available, always research and use the actual LRA value from the motor nameplate or manufacturer.
Typically, for low voltage applications the motor starter includes two components: a magnetic contactor to engage the motor, and an overload assembly, installed immediately downstream from the contactor connecting directly to the motor conductors.
Motor starters are generally classified and sized according to either NEMA or IEC standards. NEMA full voltage motor starter sizes begin at a 00 rating and continue upwards to a NEMA Size 9 rating. IEC starters are not rated or sized in the same manner, but are rated according to their specific operating environment (utilization category) and maximum motor current (amperage). Utilization categories AC3 and AC4 are the two most often applied to submersible motors.
In my judgement, since IEC starters are designed to operate at a higher temperature than comparable NEMA-rated starters, they are therefore not as robust as NEMA-rated starters, HP for HP. In order to avoid possible problems, I recommend using one or two sizes larger in current (amperage) rating for a submersible motor application when IEC-rated components are used. Refer to Table 5 for NEMA sizing of motor starters and IEC protocol.
An overload can either be a solid-state (electronic) or a thermal (current) sensing device and is designed to sense motor current on both load circuits for single-phase motors and all three load circuits for three-phase motors from either two or three separate thermal heaters or an adjustable relay that senses current in all two or three lines.
In either case, proper sizing of the device is critical to ensure the overload cannot be adjusted above the safe current level for the motor HP. All thermal overloads used for submersible motors must be ambient-compensated, quick-trip type so motor protection is provided throughout any potential change, up or down, in air temperature.
When used with a submersible motor, the overload must provide no less than Class 10 protection, which means the overload protection will trip and open the motor starter circuit within 10 seconds under locked rotor conditions to protect the motor windings.
Regardless of the type and manufacturer of the starter itself, the appropriate short circuit protection must also be provided from a properly sized and type of circuit breaker or fuses and overload protection from thermal heaters, an adjustable overload block, or a device inherent to and built into the starter, such as a VFD or soft starter.
Motor starters for medium voltage (2300 and 4160) motors are much more application and site driven than most low voltage applications. Each potential submersible motor application with medium voltage should be evaluated on a case by case basis, with the style of motor starter and protection selected only after consultation with the serving utility and motor manufacturer.
In addition to the typical methods of reduced voltage starting, submersible motors possess another unique characteristic not common to most other motor installations. Since the distance from the incoming power supply to the motor can be in many thousands of feet, including the well setting and offset run, an inherent voltage drop exists in the cable run due to the resistance in the cable.
If the total distance of cable provides the maximum 5% allowed value of voltage drop, this can result in a corresponding lowering of the starting current by up to 15% to 20%. In many cases this degree of voltage drop is sufficient to provide adequate motor starting without incurring a huge inrush of current.
It is important to note the selected motor starting mechanism is only one component of the entire motor controller. In addition to the starter, the electrical system must also include a method of disconnect and short circuit protection. Both of these comments will be discussed in greater detail in Part 4.
2.5 Pump Design Water Supply System
____________
This concludes this installment of The Water Works. In Part 4 of this series we will conclude with an expanded discussion on drop cable selection and sizing, NEC considerations, motor data and nameplate verification, motor cooling and lubrication, VFD considerations, and post-installation testing.
Water Pumping System Design
Until then, keep them pumping!
Water Pump Design Pdf
Ed Butts, PE, CPI, is the chief engineer at 4B Engineering & Consulting, Salem, Oregon. He has more than 40 years of experience in the water well business, specializing in engineering and business management. He can be reached at epbpe@juno.com.
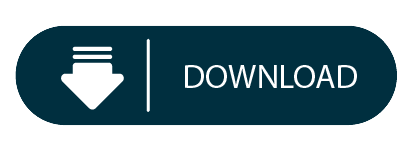